LBC: The Materials Petal
Dear Readers,
I’ll start this blog with a warning – it’s long. We of course like to make our blogs easily readable, but these ones are important because Shelby and I are also trying to understand what it takes to make a Living Building. So, you’re basically reading our research. Ok, warning out of the way, let’s do this.
Four of the seven Petals of the Living Building Challenge have been covered, Place, Water, Energy, and Health and Happiness. That leaves three to go. If you’ve read the past four blogs on their respective Petals, then you’ll know that meeting this certification will be filled with crazy challenges. We appreciate you all sticking with us as we talk through these Petals to better understand them! Believe me, we know they’re complicated. Imagine trying to figure out how to design a small house to these standards, let alone something much bigger.
To jog your memory quick, here’s that chart of all the Petals and their Imperatives:
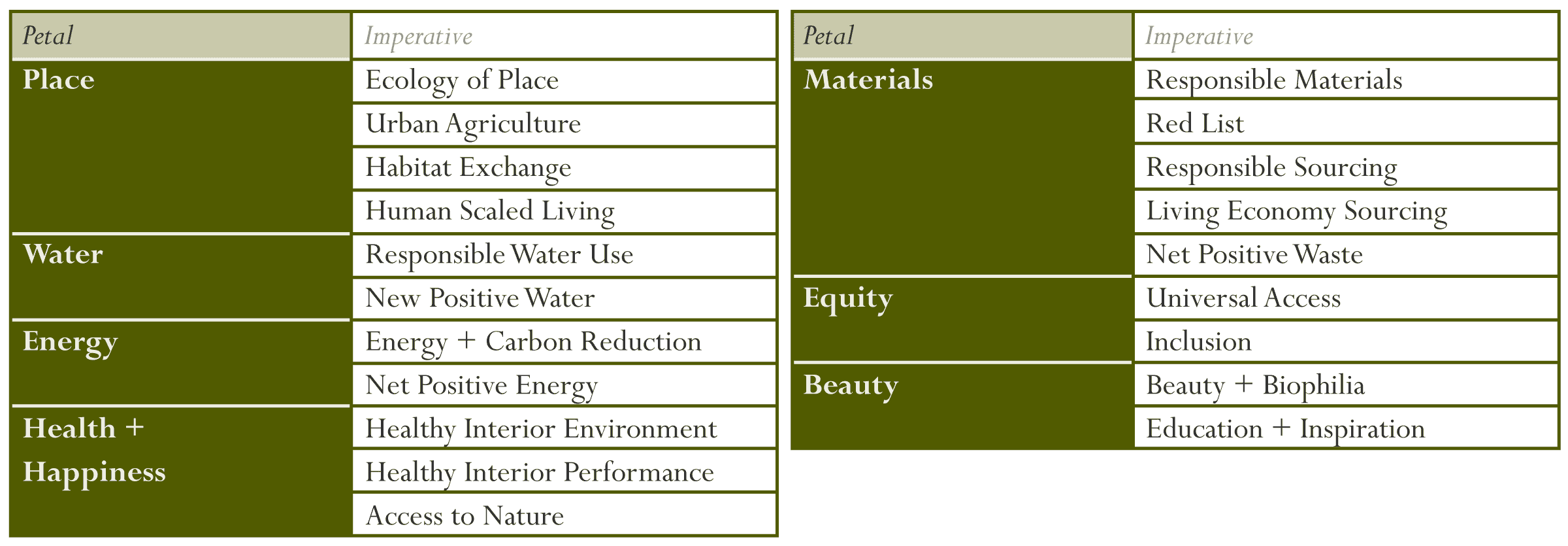
The Seven Petals of the Living Building Challenge and their Imperatives
The Materials Petal
Of the designers that have met or even tried to meet the Living Building Challenge, it’s been said that our next Petal, the Materials Petal, is the toughest. After reading this blog, you might see why. Let’s dive right into its large number of Imperatives and how Shelby and I think we might be able to pull this part of the Challenge off…

The Materials Petal and its Five Imperatives
Meeting the Responsible Materials Imperative requires a Declare label for every 200 m2 (~21,100 ft2) of gross building area and that a letter be sent to manufacturers not in Declare asking for material ingredients. It also requires one Living Product Challenge certified product (unless residential, like us). 50% of the wood products must be Forest Stewardship Council (FSC) certified, salvaged, or sustainably harvested from preparing the site for construction. Twenty percent or more of the material’s budget must be spent on materials within 500 kilometers (~310 miles) of the site. Lastly, the Responsible Materials Imperative calls for a diversion of at least 80% of the construction material from a landfill, and dedicated recycling and composting collection systems for the building occupants.1
How the Responsible Materials Imperative will impact us and The Seed:
We are actually going to skip this imperative. Not because we are lazy…but quite the opposite. We are highly idealistic, fairly naïve, over-achievers.
The Responsible Materials Imperative is essentially for projects which are not quite able to achieve full Living Building Certification. Instead of being ‘Living Building Certified,’ these projects are ‘Core Certified.’ That means that they met the most crucial, or ‘core,’ imperatives to the Living Building Challenge.
The Responsible Materials Imperative is a Core Imperative. It is basically a summarized (‘easier’ to meet) version of the remaining four Imperatives in the Materials Petal. Since Shelby and I are of course going to be idealistic and shoot for the full certification (which means we need all of the Imperatives in the Materials Petal), I’m going to skip over it and jump to the other Imperatives. If we meet the next four Imperatives, we’ll meet the Responsible Materials Imperative.
The Red List Imperative requires that at least 90% of the materials budget avoids the Living Future Institute’s Red List chemicals.2
How the Red List Imperative will impact us and The Seed:
This Imperative is short and sweet, but a real difficult one to pass. If you take a gander at the Living Future Institute’s Red List chemicals, you’ll probably recognize a lot of them – and not because you know what they all are (let’s face it, half of them are impossible to pronounce), but because these chemicals are EVERYWHERE. The Red List contains chemicals that are polluting, toxic to the food chain, and harmful to the people who handle them.3 Despite the danger they hold, these chemicals are found in soooo many things around us.
In order for Shelby and I to meet the Red List Imperative, we are going to be asking every manufacturer what their product is made out of and vetting a LOT of different products until we find the right ones. It’ll be like a scavenger hunt! I hope it’s fun. I suppose we’ll find out.
The Responsible Sourcing Imperative calls for 80% of all the project’s wood to be FSC certified, salvaged or sustainably harvested from the preparation of the site, or the project may receive FSC Project Certification. For every 200 m2 (~2,200ft2) of project area, two Declare labeled products must be used, and for every product without a Declare label, the manufacturer must be asked to register their products. For every 1,000 m2 (~10,800 ft2) of project area, one Living Product Challenge certified product must be used, or at least one for a residential project.4
How the Responsible Sourcing Imperative will impact us and The Seed:
The first part of this Imperative is a big one for us. Our house is going to use a lot of wood. We really like wood for many reasons: it’s natural and healthy, it’s beautiful, it’s a renewable resource, it’s easy to work with, it’s recyclable, it’s compostable, and it sequesters carbon. However, Shelby and I also really like trees. We’re always conflicted with the idea of letting trees grow big and beautiful, or use them to build things. This is where the Forest Stewardship Council (FSC) comes in. You can read more about them in a blog we wrote about Cross Laminated Timber, but they are a group which certifies wood products as being sustainable. They make sure loggers and manufacturers only cut down and use the trees they need in a fashion that allows a forest to stay healthy and regenerate (no clear-cutting) – so we can have trees to enjoy forever. Shelby and I are going to strive to get 100% of our wood to be FSC certified (which would allow us to get FSC Project Certification), but we need at least 80% of it to be salvaged or FSC certified in order to meet this Imperative. Oh, and any trees that we have to take down on our property to build our house, we’re going to use them or replant them.
The next stipulation of the Responsible Sourcing Imperative: use of products with a Declare Label. This is a label that you can find on any building product that is certified by the Living Future Institute. The label tells you where that product comes from, what it’s made of, and what you can do with it when it’s done being used.5 These labels are relatively new to many products, and can be hard to find. However, since Shelby and I’s house will be smaller than 200 square meters, we only need two products with a Declare Label. But that also means that we will be sending many, many letters to the other manufacturers that don’t have a Declare Label!
Since Shelby and I are designing a house, which is a residential project, we need one Living Product Challenge certified product to meet this Imperative. For a product to meet this certification, manufacturers have to go through a similar system as the Living Building Challenge with the same seven Petals, but with Imperatives that have to do with products. The certification aims to promote products that are free of toxins, respect workers’ rights, and are net positive to people and the environment.6 Shelby and I only need one of these products, but if there’s anything we need for our home that we can find with this label on it (like a standing desk), why wouldn’t we choose such a product over others? We’d love to have more than one.
The Imperative of Living Economy Sourcing refers to the project materials’ manufacturer location and states that at least 20% of the materials (by cost) come from a 500 km (311 miles) radius, at least 30% must come from a 1,000 km (621 miles) radius, and at least 25% must come from a 5,000 km (3,107 miles) radius. The remaining 25% may come from anywhere.7
How the Living Economy Sourcing Imperative will impact us and The Seed:
Let’s break this imperative down real quick to make sure it’s understood correctly. First, when it says that a certain percentage of the building materials is figured out by cost, that basically means that the total project material budget is 100% and the money spent on any one material can be divided by that number. As an example, let’s say when we’re done with our house we spend $300,000 on materials. Our windows and doors cost $40,000. We’ll divide the cost of the windows by the total materials budget (40,000 / 300,000 = 0.13) to get about 13%. So our windows and doors would account for 13% of our materials for our home. Those numbers are totally arbitrary by the way, but in case you’re curious, this house ain’t gonna be cheap!
Now the next part about the distance radii. Consider them to be cumulative. In other words, the 500 km radius is inside the 1,000 km radius which is inside the 5,000 km radius. So, another way to look at this stipulation is no less than 20% of the material’s budget must be within 500 km, no less than 50% must be within 1,000 km, and no less than 75% must be within 5,000 km.8
Shelby and I are designing a fairly unique house with a lot of systems that aren’t super popular yet. Remember those windows and doors I mentioned earlier? Passive House certification requires super specific (airtight and insulated) windows and doors, and they’re commonly found in Europe. They’re also stupid expensive. If we can’t find a great supplier of such windows and doors that’s more local, the glazing in our home could use up the whole 25% of our materials budget that’s outside the 5,000 km radius! If you know anyone that makes Passive House windows and doors within any of our radii pictured below, please put them in the comments below!9
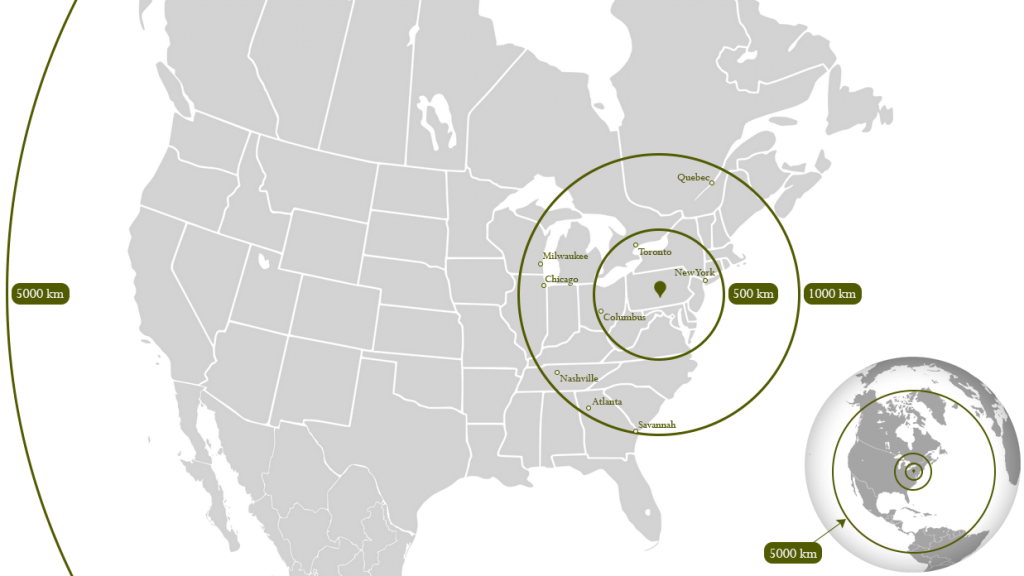
An approximate map of the Living Economy Sourcing radii distances from our project site. Some major cities are included for reference.
The Net Positive Waste Imperative requires projects to use one or more salvaged material for every 500 m2 (5,382 ft2) of building area. A Materials Conservation Management Plan must be developed to explain the optimization of materials during design, construction, operation, and end of life. Projects must also follow through with this plan and reduce or eliminate any waste through all of the aforementioned phases with the use of either an industrial or natural nutrient loop.10
How the Net Positive Waste Imperative will impact us and The Seed:
Our home will be less than 500 square meters, so we need to use at least one salvaged material (for example, reclaimed wood). We actually haven’t put much thought into this quite yet, and are not sure what that’s going to be…but I’m sure we’ll figure out something. If anyone has a brilliant idea, mention it below.
The Materials Conservation Management Plan sounds like we need to be planning now for all the “trash” we’re going to be generating during the whole life of the project. I put “trash” in quotes because I honestly believe it shouldn’t really exist and is a made-up thing we humans have invented. Shelby and I have slowly been attempting to stop producing it, and you can read about that here, but this Imperative is right in line with that belief. In other words, everything should either be reused, recycled (industrial loop) or composted (natural nutrient loop). So, while we are dreaming up this house now, we need to be thinking about everything that we’ll be using and what we’re going to do with it so that little to nothing goes into a landfill.
After we develop a plan, we need to be enacting it. While designing our home, we need to be thinking about what we’re going to be salvaging and how we can use all of whatever that is, and we need to be specifying things that will last a long time. During construction, we have to find a way to reuse, recycle, or compost all of our scrap pieces, our temporary supports, our packaging, things we break, etc. It’s very typical of a construction site to have a dumpster sitting on-site…but we’re not going to have one. Shelby and I also need systems in place to keep us from creating trash while we live in the home. For all those who come to visit us, don’t count on a trash can in the house! Maybe we’ll be lenient on our visitors though and have something like this around…
Oh, then there’s the home’s end of life: what will become of our home when no one wants to live in it anymore? It’s a really sad thought to think, but it will probably happen to every building at some point, and we need to account for that. First, we’ll make it as durable as possible so it should last for-basically-ever (remember, we’re not using sticks for our structure, we’re using cross laminated timber). After that, we’ll try to make sure that most, if not all, of our materials are either compostable or recyclable (again, wood). The last aspect to keep in mind is how the home can be taken apart. Think of the difference between gluing down a floor and letting it “float.” When you glue a floor down, like linoleum, the process of tearing it apart is usually very messy. The material tears off in chunks, and it and the stuff you glued it to are covered in, (you guessed it) glue! This makes the floor very hard to recycle or reuse. On the other hand, a floating floor is one that isn’t directly attached to the subfloor beneath it, and comes up extremely easily. Not only does this make the floor easier to reuse or recycle (along with the subfloor beneath it), but it also makes it easier to put together, fix, and replace! Check out this hardwood floor we might use – with no nails or glue – right from Central Pennsylvania!
Us, touching material things.
Alright folks! That was a long one, I know. There are a lot of Imperatives to the Materials Petal. And if you understood all of them, you might have realized how TOUGH this Petal will be, and why designers have such a hard time with it. Ideally, Shelby and I will be able to help put a lot of this together and watch over the entire process, but imagine trying to do it with a large project, with several teams! The owners, the architects, the engineers, and the contractors ALL need to be on the same page here. Everyone has to be very specific about the materials being used, substitutes need to be very carefully considered, and no one is really allowed to throw anything away! By today’s standards, it’s insane. Hopefully one day though, this may be the norm.
Thank you for sticking through to the end of this dense blog! Please feel free to give us suggestions or ideas below, or just tell us how crazy we are.
Until next time!
William Aldrich
1. International Living Future Institute. Living Building Challenge, Version 4.0, Seattle, 2019. Page 52.
2. Living Building Challenge, Version 4.0, Page 53.
3. International Living Future Institute. The Red List. Accessed 3 December 2020. The Red List | Living-Future.org (living-future.org)
4. Living Building Challenge, Version 4.0, Page 54.
5. International Living Future Institute. Declare 2.0. Accessed 3 December 2020. About Declare | Living-Future.org (living-future.org).
6. International Living Future. Living Product Basics. Accessed 3 December 2020. Living Product Basics | Living-Future.org (living-future.org).
7. Living Building Challenge, Version 4.0, Page 55.
8. Hey guys! This is Shelby 🙂 I just proofread that paragraph for William…and if you read it, like three times in a row, I promise it makes sense. Visuals also help of course.
9. On a happy note, however, we found a CLT manufacturer within the 500 km radius! Element5 Co.
10. Living Building Challenge, Version 4.0, Page 56.
5 Comments
Submit a Comment
© 2020 Sustaining Tree
© 2020 Sustaining Tree
This blog takes a lot of concentration. With that said, I need to read it again! But I am so proud of you two, and glad that young people have so much energy!
Hey Aunt Rose, thank you for reading! This was definitely a tough one to wrap our heads around, and now we have to apply it to our designs! Hopefully we’ll have enough energy to keep this thing going!
Pella is planning a new plant in Troy, OH.
The Pella 350 Series triple pane window is pre-certified on a project on the phius.org website.
See the hook and ladder project #1499 on the certified projects database.
This is definitely worth looking into, I didn’t know Pella was making high-performance windows. Thank you Frank!